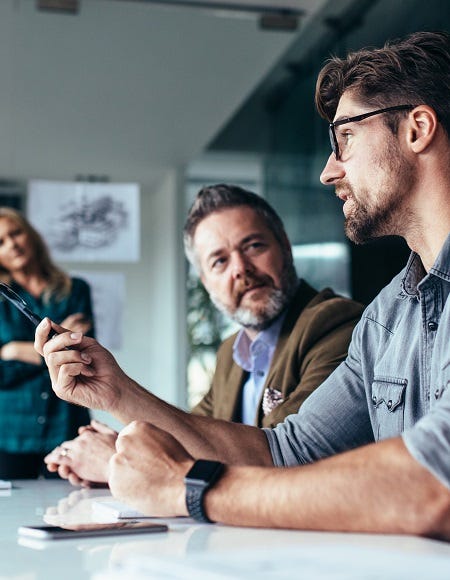
Fehlermöglichkeits- und Einflussanalyse – dem Fehler frühzeitig auf der Spur.
Die Fehlermöglichkeits- und Einflussanalyse (FMEA) ist eine methodische Herangehensweise, um potenzielle Risiken in Prozessen, Produkten oder Systemen frühzeitig zu identifizieren und zu bewerten. Sie spielt eine entscheidende Rolle in der Qualitätssicherung. In diesem Beitrag lernen Sie die Basics zur FMEA kennen. Sie erfahren, wie die FMEA umgesetzt wird und warum die Zusammensetzung des FMEA-Teams ein wesentlicher Erfolgsfaktor dieser Methode ist.
Was ist eine Fehlermöglichkeits- und Einflussanalyse (FMEA).
Die Fehlermöglichkeits- und Einflussanalyse (FMEA – englisch: Failure Mode and Effects Analysis) ist eine systematische Methode zur Identifizierung und Bewertung von potenziellen Fehlern in einem Prozess, System oder Produkt. Ziel der FMEA ist es, frühzeitig mögliche Schwachstellen zu erkennen, um präventive Maßnahmen zu ergreifen und die Wahrscheinlichkeit von Fehlern zu reduzieren oder zu verhindern. Durch eine strukturierte Analyse von Fehlerquellen, ihrer Auswirkungen und der Wahrscheinlichkeit ihres Auftretens ermöglicht die FMEA eine proaktive Risikobewertung und trägt zur Verbesserung der Produkt- oder Prozessqualität bei.
Die FMEA wurde in den 1940er Jahren entwickelt und erstmals in der Luftfahrtindustrie der Vereinigten Staaten angewendet, später von der NASA.
In den folgenden Jahrzehnten entwickelte sich die FMEA weiter und fand Anwendung in verschiedenen Bereichen, darunter u.a. die Automobilindustrie, Medizintechnik oder Elektronik- und Halbleiterindustrie. Die Analyse hat sich zu einem wichtigen Instrument in der Qualitätssicherung und der Risikobewertung etabliert und wird heute weltweit in vielen Industriezweigen durchgeführt.
Welche Vorteile bietet die Fehlermöglichkeits- und Einflussanalyse?
Die FMEA bietet eine Vielzahl von Vorteilen für Unternehmen.
Reduzierung von Fehlern und Risiken
Die FMEA ermöglicht eine proaktive Identifizierung von potenziellen Fehlern durch die systematische Analyse von möglichen Fehlerquellen. Durch diese frühzeitige Erkennung können präventive Maßnahmen ergriffen werden, um die Wahrscheinlichkeit des Auftretens von Fehlern zu reduzieren oder sie sogar vollständig zu vermeiden. Dies trägt dazu bei, kostspielige Fehler in späteren Phasen des Projekts zu verhindern und fördert eine reibungslosere Umsetzung von Prozessen oder die Entwicklung von Produkten. Das Risiko von Qualitätsproblemen wir dadurch reduziert.
Kostenersparnis
Durch die Beseitigung von Fehlern in frühen Phasen des Entwicklungsprozesses können erhebliche Kostenersparnisse erzielt werden. Es ist kosteneffizienter, Probleme frühzeitig zu lösen, als spätere Korrekturen während der Produktion vorzunehmen oder gar nach Markteinführung. So besagt zum Beispiel die auf Erfahrungswerten basierende Rule-of-Ten (Zehnerregel der Fehlerkosten), dass die Kosten für die Fehlerbehebung in jeder einzelnen Stufe der Wertschöpfungskette um den Faktor 10 steigen. Die Kosten zur Fehlerbehebung steigen überproportional an, wenn der der Fehler nicht bereits in der Planung, sondern erst in der Entwicklung (x10), in der Produktion (x100) oder sogar beim Kunden (x1.000) entdeckt wird.
Qualitätssteigerung
Die systematische Analyse der FMEA trägt dazu bei, die Gesamtqualität von Produkten oder Prozessen zu verbessern, was wiederum die Kundenzufriedenheit steigert. Durch Wiederholung der FMEA in regelmäßigen Abständen, wird eine kontinuierliche Verbesserung von Prozessen und Produkten im Laufe der Zeit ermöglicht.
Erfüllung von Standards und Vorschriften
Die FMEA unterstützt dabei, von Anfang an sicherzustellen, dass das entwickelte Produkt den geltenden Standards und Vorschriften entspricht. Dies verhindert Verzögerungen, die durch nachträgliche Anpassungen zur Einhaltung von Vorschriften entstehen könnten. Darüber hinaus sind z.B. in der Automobilindustrie die sogenannten Automotive Core Tools – darunter auch die FMEA – fester Bestandteil eines IATF 16949-basierten QM-Systems.
Welche Varianten der FMEA gibt es?
Die Fehlermöglichkeits- und Einflussanalyse (FMEA) kann in verschiedenen Kontexten angewendet werden. Es gibt drei Hauptvarianten:
- System-FMEA (SFMEA): Die System-FMEA konzentriert sich auf die Analyse von potenziellen Fehlern auf der Ebene des Gesamtsystems. Dies bezieht sich auf die Identifizierung von Risiken und möglichen Fehlern, die das Gesamtsystem oder das Endprodukt beeinflussen könnten.
- Design-FMEA (DFMEA): Die Design-FMEA bezieht sich auf die Analyse von potenziellen Fehlern auf der Ebene des Designs oder der Produktentwicklung. Ziel ist es, Fehler zu identifizieren, die während des Designs auftreten könnten und die die Funktionalität oder Sicherheit des Produkts beeinträchtigen würden.
- Prozess-FMEA (PFMEA): Die Prozess-FMEA konzentriert sich auf die Analyse von potenziellen Fehlern auf der Ebene des Herstellungs- oder Produktionsprozesses. Ziel ist es, Schwachstellen im Prozess zu identifizieren, die zu Fehlern im hergestellten Produkt führen könnten.
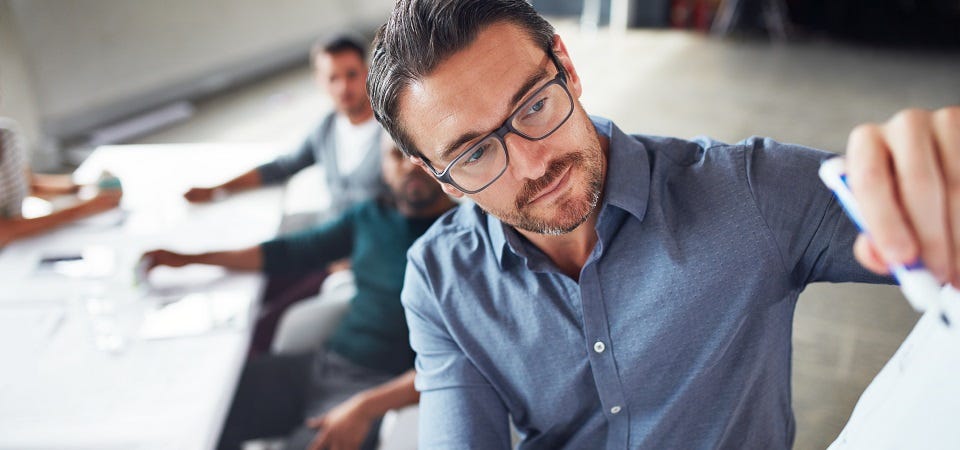
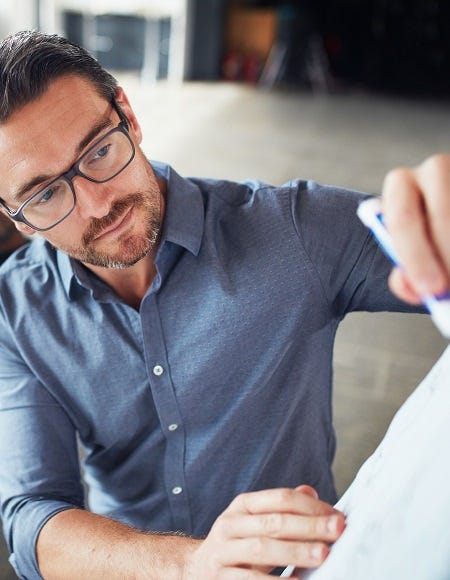
Das Team als Erfolgsfaktor der FMEA.
Das Team spielt eine entscheidende Rolle für eine erfolgreiche FMEA, da verschiedene Perspektiven und Fachkenntnisse erforderlich sind, um eine umfassende Analyse durchzuführen. Teammitglieder bringen ihre individuellen Erfahrungen und Expertise aus unterschiedlichen Bereichen ein, um sicherzustellen, dass alle relevanten Aspekte berücksichtigt werden. Die Vielfalt im Team ermöglicht eine ganzheitliche Betrachtung der potenziellen Risiken.
Das optimale FMEA-Team sollte aus einem Kern- und einem erweiterten Team bestehen. Idealerweise besteht das Kern-Team neben dem Projektleiter aus 4 bis 6 Personen. Diese werden sorgfältig ausgewählt, basierend auf dem Beitrag, den sie zu der spezifischen FMEA leisten können. Ein FMEA-Team sollte einen Querschnitt der Organisation in Bezug auf die funktionale Verantwortung repräsentieren
Die Rollen und Funktionen im FMEA-Team.
Auftraggeber
Der Auftraggeber ist verantwortlich für die Initiierung der FMEA. Er hat entscheidenden Einfluss auf die Definition des FMEA-Umfangs.
Projektleiter
Der FMEA-Projektleiter plant und koordiniert die FMEA-Aktivitäten. Er stellt sicher, dass alle notwendigen Ressourcen zur Verfügung stehen und dass der FMEA-Prozess im festgelegten Zeitrahmen abgeschlossen wird. Der Projektleiter führt das Team und motiviert die Teammitglieder. Er sorgt dafür, dass alle Mitglieder ihre Aufgaben verstehen und erfüllen. Es ist die Hauptkontaktperson für das FMEA-Team und kommuniziert regelmäßig mit dem Management sowie anderen Stakeholdern über den Fortschritt der FMEA.
Moderator
Der FMEA-Moderator leitet die FMEA-Sitzungen. Er fördert die Zusammenarbeit und Kommunikation innerhalb des Teams und stellt sicher, dass alle Teammitglieder ihre Ideen und Bedenken äußern können. Der Moderator hält das Team auf das Ziel der FMEA fokussiert, nämlich die Identifikation und Minimierung von Risiken. Er zeichnet dafür verantwortlich, dass die FMEA-Methode korrekt angewendet wird und dass alle notwendigen Schritte durchgeführt werden. Zu seine Aufgaben zählt es auch, das Team in der Anwendung der FMEA-Methode zu schulen.
Fachexperten
Fachexperten bringen spezifisches Wissen in das Team ein, das für die Durchführung der FMEA notwendig ist. Dies können beispielsweise Ingenieure, Designer, Qualitätsmanager oder Produktionsmitarbeiter sein. Es müssen nicht alle zwingend über umfassende Kenntnisse der Konstruktion oder des Prozesses verfügen, auf den sie abzielen. In der Tat hilft es manchmal, die frische Perspektive eines Außenstehenden zu berücksichtigen.
Zusätzlich zum Kern-FMEA-Team sollte es auch eine Unterstützungsgruppe von Personen geben, die das Kern-Team bei Bedarf an Fachwissen, Einblicken und Anleitung hinzuziehen kann. Dieses erweiterte Team kann aus weiteren Fachexperten, Bedienern, Anwendern des Produkts oder des Prozess-Outputs bestehen.
Kunden- und Nutzervertreter
In einigen Fällen kann es auch hilfreich sein, einen Kunden- oder Nutzervertreter in das Team aufzunehmen, um die Perspektive des Endbenutzers in die FMEA einzubringen.
Dokumentationsverantwortlicher
Der Dokumentationsverantwortliche ist dafür verantwortlich, alle Schritte der FMEA zu dokumentieren und sicherzustellen, dass die Dokumentation vollständig und genau ist.
Die 7 Schritte der FMEA.
Die Fehlermöglichkeits- und Einflussanalyse (FMEA) wird strukturiert und systematisches in sieben Schritten durchgeführt. Die folgenden 7 Schritte beziehen sich auf eine Prozess-FMEA.
1. Planung und Vorbereitung
In der ersten Phase, der Planung und Vorbereitung der Prozess-FMEA, werden die Grundlagen für eine systematische Analyse gelegt. Dies beinhaltet die Festlegung klarer Ziele, den definierten Umfang des zu betrachtenden Prozesses und die Auswahl eines multidisziplinären Teams von Experten. Die Planung umfasst auch die Zuweisung von Ressourcen, die Festlegung von Zeitrahmen und die Definition von Verantwortlichkeiten.
2. Strukturanalyse
Die Strukturanalyse widmet sich der systematischen Zerlegung des betrachteten Prozesses. Hierbei werden sämtliche Komponenten und Teilschritte identifiziert und in einer hierarchischen Struktur abgebildet. Dies ermöglicht einen detaillierten Überblick über den Aufbau des Prozesses und legt die Grundlage für die folgenden Analyseschritte.
3. Funktionsanalyse
Die Funktionsanalyse konzentriert sich auf die Ermittlung der Funktionen jeder einzelnen Komponente des Prozesses. Hierbei werden nicht nur die grundlegenden Aufgaben betrachtet, sondern auch die Wechselwirkungen und Abhängigkeiten zwischen den verschiedenen Komponenten analysiert. Das Verständnis der Funktionalitäten ist entscheidend für die Identifikation von potenziellen SchwachstellenIn der Fehleranalyse werden mögliche Fehlerquellen innerhalb des Prozesses ermittelt. Dies umfasst sowohl bekannte als auch hypothetische Fehler. Die gründliche Fehleridentifikation ermöglicht es, Schwachstellen zu erkennen und ihre potenziellen Auswirkungen auf den Gesamtprozess zu bewerten.
4. Fehleranalyse
In der Fehleranalyse werden mögliche Fehlerquellen innerhalb des Prozesses ermittelt. Dies umfasst sowohl bekannte als auch hypothetische Fehler. Die gründliche Fehleridentifikation ermöglicht es, Schwachstellen zu erkennen und ihre potenziellen Auswirkungen auf den Gesamtprozess zu bewerten.
5. Risiko- und Maßnahmenanalyse
Die Risiko- und Maßnahmenanalyse bewertet die identifizierten Fehler hinsichtlich ihrer Risikoprioritätszahl (RPZ). Diese Kombination aus Eintrittswahrscheinlichkeit, Entdeckungswahrscheinlichkeit und Schweregrad ermöglicht eine gezielte Priorisierung der Risiken. Auf Grundlage dieser Bewertung werden präventive oder reaktive Maßnahmen entwickelt, um die kritischen Risiken zu minimieren.
6. Maßnahmenumsetzung
In diesem Schritt werden die zuvor identifizierten Maßnahmen zur Risikominderung implementiert. Das kann die Anpassung von Prozessschritten, Schulungen von Mitarbeitern oder die Einführung neuer Technologien umfassen. Eine enge Zusammenarbeit zwischen den verschiedenen Abteilungen ist entscheidend, um sicherzustellen, dass die Maßnahmen effektiv umgesetzt werden.
7. Dokumentation
Die umfassende Dokumentation ist entscheidend, um den gesamten Prozess der Prozess-FMEA nachvollziehbar zu gestalten. Hierzu gehören alle durchgeführten Analysen, identifizierten Risiken, ergriffenen Maßnahmen sowie die Ergebnisse der Risikobewertung. Die Dokumentation dient nicht nur der Transparenz, sondern auch als Basis für zukünftige Analysen und Qualitätsverbesserungen.
Kontinuierliche Überprüfung.
Die Prozess-FMEA ist ein dynamisches Instrument, das regelmäßig aktualisiert werden muss. Neue Erkenntnisse, Veränderungen im Prozess oder technologische Weiterentwicklungen können neue Risiken mit sich bringen. Daher ist eine kontinuierliche Überprüfung und Aktualisierung der FMEA notwendig, um sicherzustellen, dass sie immer auf dem neuesten Stand ist und effektive Risikominimierungsmaßnahmen enthält.
Fazit.
Die Fehlermöglichkeits- und Einflussanalyse ist ein mächtiges Instrument, um die Qualität von Produkten und Prozessen zu gewährleisten. Durch eine sorgfältige Durchführung und kontinuierliche Aktualisierung können Unternehmen potenzielle Risiken minimieren und eine höhere Kundenzufriedenheit erreichen.
Eine proaktive Haltung gegenüber Qualitätsmanagement und kontinuierliche Verbesserung ist entscheidend, um in einer sich ständig wandelnden Geschäftsumgebung erfolgreich zu sein.
Empfehlung.
In der TÜV Rheinland-Weiterbildung Fehlermöglichkeits- und Einflussanalyse (FMEA) lernen Sie anhand von Praxisbeispielen eine FMEA systematisch anzuwenden und auszuwerten. Das Tagesseminar liefert Ihnen das notwendige Know-how, um aus den Ergebnissen der FMEA Folgemaßnahmen zur Fehlervermeidung abzuleiten.